By Nicole Sawyer, Bloomberg Live
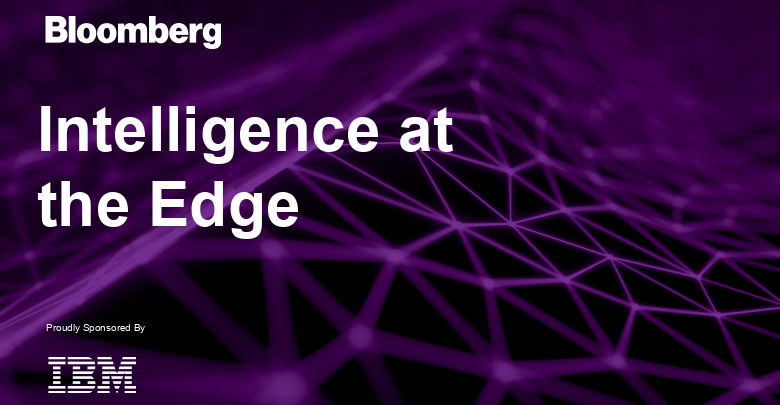
Intelligence at the Edge Roundtable:
How Manufacturers Can Accelerate Digital Transformation
To compete in a changing world, manufacturing operations are becoming Digital Manufacturing Enterprises, utilizing emerging technologies including artificial intelligence; robotic. 3-D printing, automation, augmented reality and cloud capabilities. The pandemic has further accelerated the need for agile supply chains and for businesses to make digital transformation in manufacturing a priority. Big data analytics are essential to manufacturing operations to discover new information, improve processes and increase supply chain efficiency. The ability to bring analysis to the edge and circumvent the cloud could further enhance productivity.
From 5G to edge computing to hybrid cloud and sustainable processes, how are leaders utilizing advanced manufacturing techniques to navigate challenges and how will these enhance business models in the future?
During the Bloomberg roundtable, we spoke directly with senior leaders about how they expect business models to evolve as growing numbers of manufacturing companies look to embark on this transformative journey.
Here’s what they had to say:
PARTICIPANTS
Rob Bodor, Vice President and General Manager, Americas Protolabs
Alicia Hammersmith, Senior Operations and Supply Chain General Manager at Wabtec
Tami Hedgren, Manufacturing Lead, Combines & Tractors. John Deere
Joel Honeyman, Vice President of Global Innovation, Doosan Bobcat
Matthias Liden, Head of Group Supply Americas Ericsson
David Meek, Partner, IBM Global Business Services
Mark Russell, Raytheon Technologies CTO & Senior Vice President
Raja Shembekar, Vice President, N.A. Production Innovation Center DENSO International America, Inc.
Bissell Smith, Aerion Corporation Chief Information Officer and EVP Enterprise System
Ann Tracy, Chief Suitability Officer, Colgate-Palmolive
MODERATED BY
Anurag Rana, Bloomberg Intelligence Senior Analyst
Click here to view video of the full discussion.
Cloud vs. edge: a hybrid model emerging
Intelligence at the Edge: How Manufacturers Can Accelerate Digital Transformation, Bloomberg’s virtual roundtable, kicked off with senior global executives’ discussing how manufacturers can accelerate digital transformations and computing at the edge with 5G to unlock value from data in real time, optimize operations and transform their organizations in a post-Covid-19 world.
Raja Shembekar, Vice President, N.A. Production Innovation Center DENSO International America, Inc., discussed a hybrid model from cloud to on-premise that’s emerging right now. “Initially everybody rushed to cloud computing. That was the in thing to do. But they quickly realized that the cloud is expensive. It costs money to upload, costs money to download,” Shembekar said.
Video analytics, images and video cannot be compressed, thus causing latency issues, and larger amounts of data are required to process these files — therefore companies turned to edge. Shembekar pointed out that edge has its risks and asset management can be a big problem. “Edge computing is an asset. That means you own it and you have to maintain it,” he said. “So it has its benefits. But you need to look at who is going to maintain this equipment. And that becomes a big issue. And do they have the skill set to maintain these systems?”
He added, “People that require very low latency because of data size or if there are cybersecurity or risk issues, they go to the edge. And those that have high compute requirements basically go to the cloud.”
Mark Russell, Raytheon Technologies CTO & Senior Vice President, explained that winners or losers will be determined by who makes architectural decisions correctly.
“We recently did the upgrade to the GPS systems worldwide, all the ground stations,” he said. “So architecturally we have to separate the cloud from millions of lines of software, but also then we have to control the satellites and handle things in milliseconds. A lot of times a cloud is determined by what you’re doing, the architecture and where is it reasonable to do functions? And that’s changing dramatically with the advancement of microprocessors. And we’re shifting back to so much processing being able to be done at the edge that it is changing architectures.”
He added, “You’ve got to be careful how you set up your architecture, and secondly that your architecture sets up for timing. 5G will get you down to milliseconds, but milliseconds are used for certain precious amounts of bandwidth. And it’s got to be for things like positioning satellites or moving slice network data between the kid in the back seat downloading movies versus safety in a car where you’ve got to make sure that you have an airbag because somebody might hit you.”
Rob Bodor, Vice President, and General Manager, Americas Protolabs, explained that a combination of technologies can take time and cost out of the manufacturing processes and enable agility in the supply chain in ways that we couldn’t have achieved before.
“Digital twins, the cloud, A.I. and the analytics around the industrial IoT, along with the edge computing can provide tremendous agility. And we’ve seen that recently with the disruption around Covid. We had the opportunity to make eight million parts in the last several months in a matter of days with response times for our customers and things like face shields, ventilators, test kits all because of how we’ve created agility within our manufacturing process to be able to meet those needs at a time of significant volatility,” he said.
Before joining Aerion Corporation as Chief Information Officer and Executive Vice President for Enterprise System, Bissell Smith served as an executive at a large aerospace company, Northrop Grumman, for 35 years. Smith pointed out the benefits and challenges of adopting technology as a start-up. “As a start-up company, it’s a very different perspective. You don’t have a lot of legacy infrastructure that bogs you down. You don’t have all the issues that come along with trying to make a change and the high cost associated with making a change when you have all your platforms already established,” he explained.
Smith said Aerion Corporation is in the preliminary design review (PDR) phase of the[C3] aircraft and it was critical to do most of the high-performance computing (HPC) in the cloud from a schedule standpoint because the company was able to do very intensive computing compared with using their HPC environment. However, the cloud method became “quite expensive.”
He said, “As Covid-19 hit the environment, we had to switch back to mainly our on-premise system and try to increase the computing capabilities of it.”
Smith also said that as he builds out the manufacturing environment for Aerion, the edge will be part of their architecture, but one of his biggest challenges is putting together architecture that allows Aerion to collaborate with partners such as Boeing, General Electric and Spirit.
Unlocking value from data
Tami Hedgren, Manufacturing Lead, Combines & Tractors for John Deere, said, “On the shop floor what matters is a supervisor, a manufacturing engineer, a quality engineer getting the right data, at the right time, with different means to do it. But we want that seamless to them to put them in the right spots to be proactive on some of these key issues. So you’ll see us continue to use the cloud and look for other alternatives. We’ve done some testing with 5G as well.”
Joel Honeyman, Vice President of Global Innovation at Doosan Bobcat, said his company has taken a hybrid approach to unlock data. “We just put telematics standard on all of our equipment, so we have one hundred thousand connected assets in the field and, obviously, that makes sense to go in the cloud,” he said.
“But now when we’re doing big data analytics and we want to analyze that data maybe with our manufacturing data or warranty data, we left that in the current systems and we’re just using some different ways to pull that information in because we just found it didn’t make sense to make all of that investment right now to move those systems into the cloud today.”
Matthias Liden, Head of Group Supply Americas at Ericsson, explained a big problem he faces is thinking through the process to make data accessible to solve major problems. “I do a lot of data plumbing, as we call it, and put that into data lakes independent of the process where it might come from in the manufacturing,” he said. “So now I need to think about who should have the right to release data, who should have access to this data?
“You want to have people play around with the data to seek solutions from the data. At the very start when we design our new data lakes, I need to think about what kind of uses I may have to do in the future. I want to enable it as well. I don’t just want to restrict it,” he added.
Creating a culture of continuous improvement
Putting technology aside, all of the participants agreed that the most important element critical to a company’s success is to create the right culture of continuous improvement and put a structure in place that empowers leaders at all levels to make use of data and make the right decisions.
Ann Tracy, Chief Suitability Officer for Colgate-Palmolive, said access to data is what allowed her company to focus during the Covid-19 crisis — and a huge focus for her company is to change the mindset and empower employees.
“Being able to focus and make decisions allowed us to keep our sustainability program going full speed ahead. In some cases, even accelerate our programs around environmental efficiencies — whether it’s energy or water reduction,” she said. “We have not missed a beat and I don’t think we could have done that without the suite of tools that we’ve had.”
Alicia Hammersmith, Senior Operations and Supply Chain General Manager for Wabtec, said, “You may not have all the data, you may have 80 percent and that may be good enough to make the right business decision. I do think it’s about the skills, the mindset, the training of how do we use the data. We have to make the best decisions without looking for perfection because we’ll never get there.”
Hedgren said changing teams’ skill sets throughout the manufacturing plant and helping them see the possibilities remains the biggest challenge. “The major difference for us is the chance to test out,” she said. “It’s really about the stack and understanding the pain points to be able to drive it to the next level. We’ve been doing some testing with 5G and we see the huge benefits. Instead of in a factory having drops that are twelve hundred dollars each, now it’s real-time data where you need it at the right time and it’s a completely different viewpoint than Wi-Fi. The biggest challenge is upskilling.”
Future ready supply chains
The future of the global supply chain has been uncertain — with the tariff war and tensions between the U.S. and China escalating even before Covid-19. Participants discussed where their bottlenecks are and how they plan to change the way they operate to create agile supply chains moving forward.
DENSO International has operations in almost every corner of the planet. Shembekar said he’s using wireless sensor technology to combat bottlenecks, “This IoT smart sensor monitors intermodal, so it doesn’t matter whether your product is coming from the plane or the ship or the train,” he said. “It provides continuous real-time data and visibility of where your product is until it reaches it.[C6] And not only that, it provides an ETA when it’s going to arrive. And the costs of implementing such kind of technologies are becoming so affordable that I think wireless sensor technology is the way to go from a supply chain standpoint.”
Doosan Bobcat’s Honeyman said, “We’ve done some things to simplify things for manufacturing with less configurations at our factories. And we rolled out features on demand this year. And so we’re able to push that closer to the dealer and the customer where they can custom configure their machines the way they would like them closer to where they are and that frees up our manufacturing to build more standardized types of products. Covid accelerated that development along the way for us to look at our business in that way.”
Hammersmith said, “We have large industrial products and then your customers are accustomed to it’s a requirement that they come in and they sign off on the product. That’s typical with large industrial equipment. So we had the other issue where we had product piled up and customers were unable to travel into our sites. And this is global, all of our locations. So we had to very quickly change our terms and conditions to work with our customers to do video acceptance. So it was really not just within our supply chain but even extending out to our customers.”
David Meek, Partner, IBM Global Business Services, said, “We have global plants and, in our mainframe, for example, it might take over 30,000 different individual electronics pieces before we have a finished product out the door. And, like many of the companies have stated, you know we have all sorts of tracking of both inbound and finished goods outbound. What’s different is we’ve applied Watson and AI to look for early disruptions so that we can proactively source other components from maybe completely different suppliers so that we can meet the customer’s order on demand. And then we facilitate that by creating a resolution room and we pull in the two, three, four people from across our supply chain that can quickly resolve it and then provide them the data so that the key is getting the data to the right people at the right time so they can make the right decisions and keep things moving.”
——————————
Instagram: @BloombergLive
LinkedIn: Bloomberg Live
Twitter: @BloombergLive
Interested in more Bloomberg Live virtual events? Sign up here to get alerts.
——————————